O-Rings are vital to sealing applications, and their failure can lead to system downtime and safety risks. In this blog, we address the most common reasons behind o-ring failures and offer practical solutions. From compression set issues to chemical attacks and temperature variations, we explore the challenges o-rings face and provide insights to ensure these seals perform reliably in your applications. By the end of this guide, you’ll be well-equipped to prevent o-ring failures and maintain system integrity1. Compression Set:
1. Compression Set
Problem Sources:
- Selection of an elastomer with poor compression set properties.
- Low heat resistance.
- Excessive swelling of o-ring in system fluid.
- Too much squeeze.
- Incomplete curing during production.
- High operating temperature.
Possible Solutions:
- Select a low set elastomer with better compression set properties.
- Choose an o-ring material resistant to both operating and friction-generated heat.
- Verify compatibility of o-ring material and system chemicals.
- Reduce squeeze if possible.
- Inspect o-rings for quality prior to installation.
- Use a higher temperature-rated material.
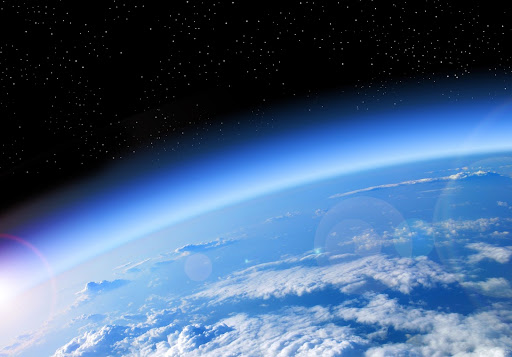
2. Weather or Ozone Cracking
Problem Source:
- Ozone breaking down polymer chains.
- Higher concentrations around electronics. Also, in atmospheric air.
Possible Solution:
- Employ o-ring elastomers that are resistant to ozone attack
3. Installation Damage
Problem Sources:
- Sharp edges on mating components of the o-ring gland.
- Sharp threads over which the o-ring must pass during assembly.
- Insufficient lead-in chamfer.
- Oversized o-ring ID on the piston.
- Undersized o-ring ID on the rod.
- Twisting or pinching of the o-ring during installation.
- Lack of lubrication during installation.
Suggested Solutions:
- Break all sharp edges.
- Cover threads with tubes or tape during o-ring installation.
- Provide a 15-20° lead-in chamfer.
- Use lubrication during the installation process.
- Ensure correct sizing of o-rings.
4. Incorrect O-Ring Size
Suggested Solution:
- Ensure that o-rings have the correct dimensions to prevent incomplete seals. You can use tools like Apple Rubber’s O-Ring Gland Calculator or consult their engineering department to simplify the process of finding and ordering the exact o-rings you need.
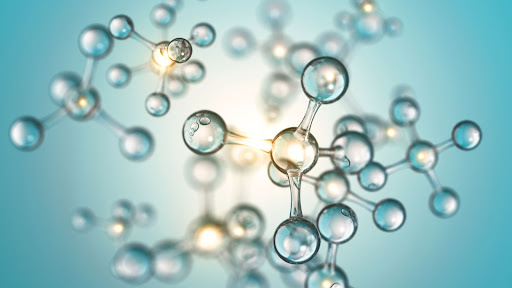
5. Chemical Exposure
Problem Source:
- Exposure to harsh chemicals and solvents that can degrade the o-ring material over time.
Possible Solutions:
- Select o-ring materials that are compatible with the chemicals and fluids in the system.
- Consider using chemically resistant elastomers like Viton for applications involving aggressive chemicals.
- Implement regular inspections and replacements when necessary to prevent degradation over time.
6. Excessive Temperature Variations
Problem Source:
- Rapid and extreme temperature fluctuations can cause o-rings to expand and contract, leading to material fatigue and reduced sealing effectiveness.
- High temperature can cause plasticizers to come out and additional cross linking which will make the rubber harder and more brittle.
- Low temperatures pass glass transitions of the rubber can cause excessive compression set.
Possible Solutions:
- Choose o-ring materials with a wide temperature range suitable for the application.
- Implement temperature controls or insulation to minimize rapid temperature changes in the system.
- Use backup rings or additional support components to reduce the stress on o-rings in high-temperature variations.
Preventing o-ring failures is essential to maintain the integrity of seals in various applications. Proper material selection, installation procedures, and quality control are key to ensuring o-rings perform as intended.